PDC Machines is committed to a cleaner, greener, and more equitable future. To that end, we’ve developed a suite of cutting-edge technologies, supported by our manufacturing capabilities and first-class employees. We are guided by rigorous environmental, social, and governance standards that reflect our values as a company. Read on to find out about our capabilities and commitments.
Mission Statement
Provide comprehensive solutions for our customers’ unique needs. Through our Core Values of Purpose, Loyalty, and Humility we commit ourselves to excellence and are dedicated to giving our customers, employees, and community the best.
Core Values
Purpose ∙ Loyalty ∙ Humility
Customer Centered Approach
Confidence ∙ Pride ∙ Respect
Foundation Principles
Innovation ∙ Education ∙ Responsiveness
Customer Support
PDC Machines provides outstanding customer support for all our clients. Our compressors are backed by a veteran team of sales engineers, project engineers, factory service technicians, and a global support network to ensure maximum uptime of our customer’s operations.
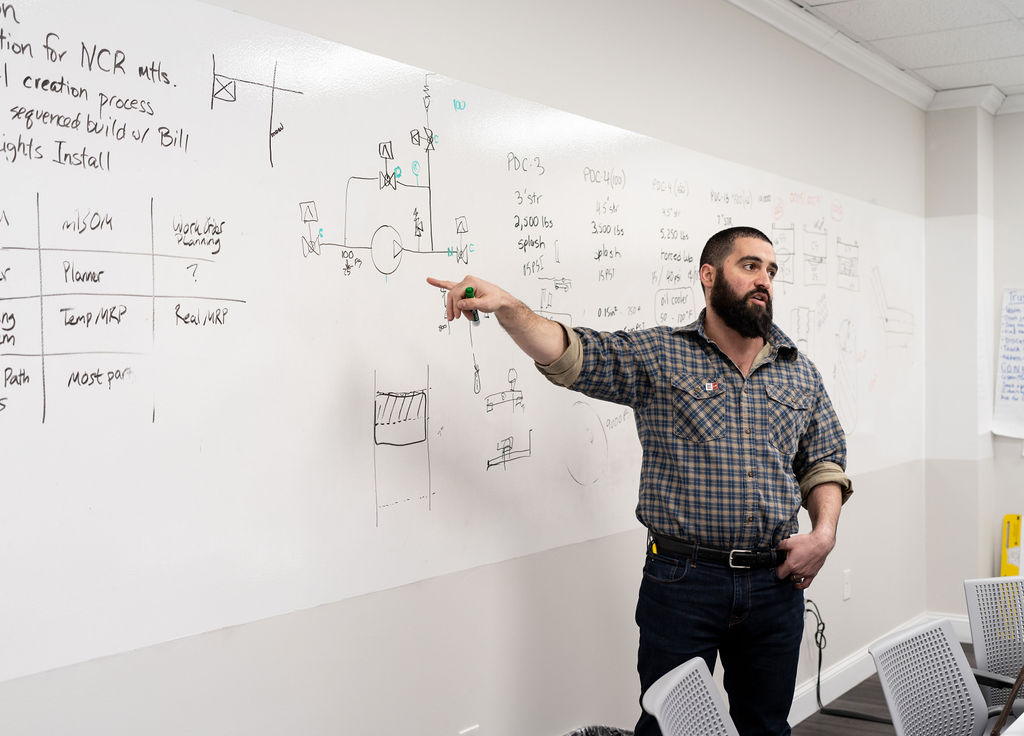
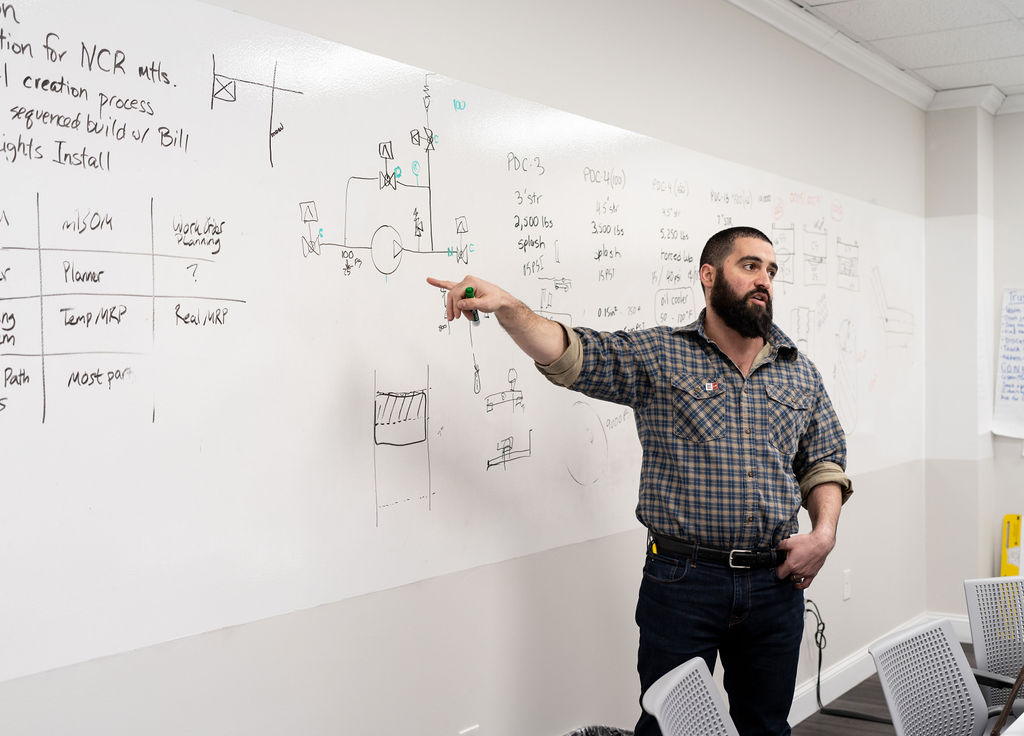
The Industry Leader in Compressor Installations
600+
Customers Served
Installations Across
56 Countries
6 Continents
Approx.
2000
Compressors
Delivered Since 2010
900
of which are
Alternative Energy Stations
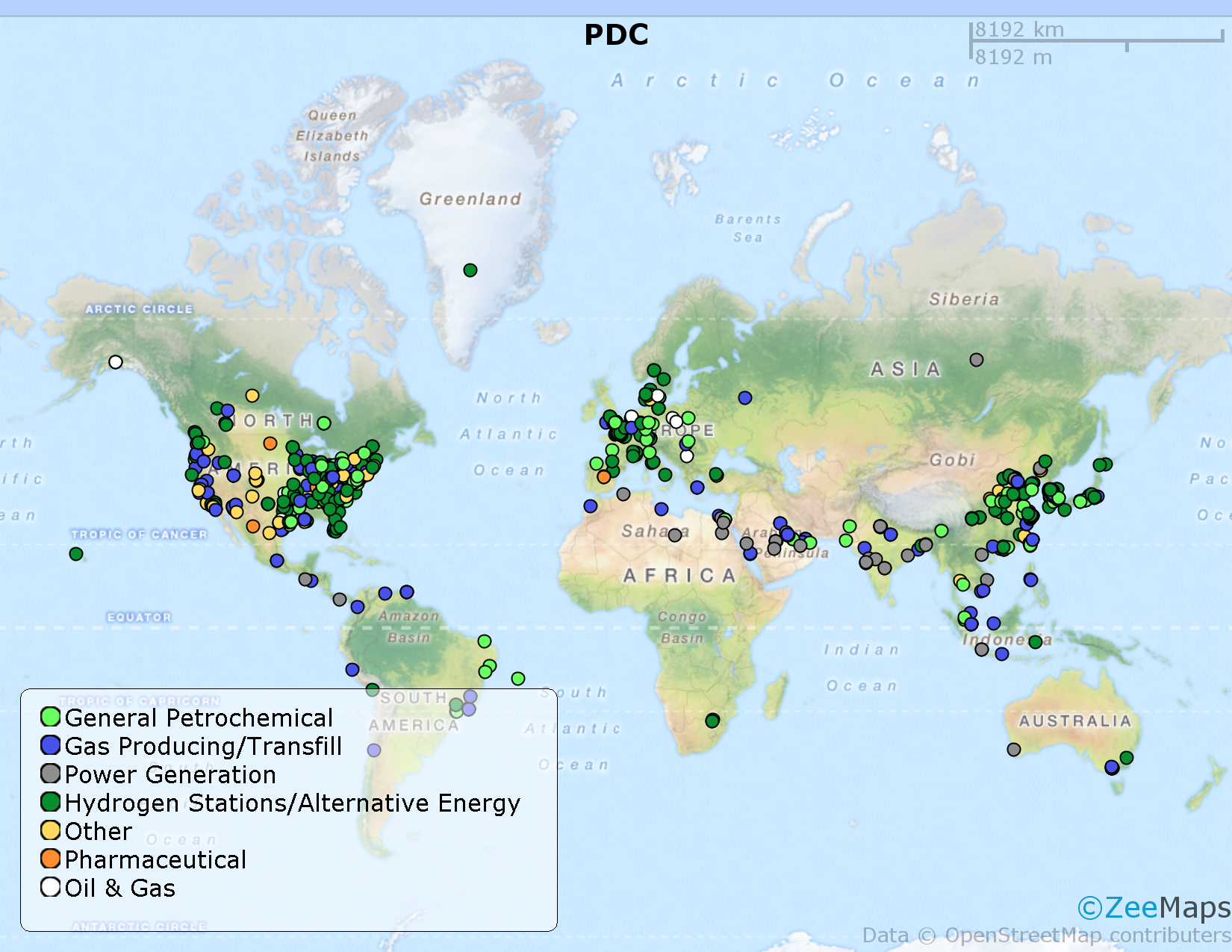
The Industry Leader in Installations
Bennett Waterhouse, Air Liquide
I am taking the time to write this thank-you letter to PDC because of the incredible customer support we received when we were in need.
I have never had to ask PDC to do any service or rush any parts on any of the 6 PDC compressors I have bought in the last 14 years. This is because your units have always run as expected and we have always had your recommended critical parts in stock. We had never previously experienced a failure on any of these units.
Our recent crisis came about because of an undiagnosed failure of our heat tracing, combined with a concurrent process upset. These conditions led to extreme cold, causing compressor oil thickening, causing higher than normal vibration. These excessive vibrations led to an unrecognized oil leak. The oil leak eventually caused cavitation in one of the compressors, which led to a failure of lower end parts.
We were not able to properly diagnose this problem until we had Wayne come out to our site. He led us through a regimented troubleshooting approach, which led us to find that we needed to replace the entire lower end and crankcase. This was, of course, on a Friday afternoon.
This failure showed the main safety and quality reason that we use your diaphragm compressors, even with a lower end mechanical failure, caused by cavitation, leading to extreme vibration; we never experienced any process leaks to atmosphere or any mixing of oil and process gas.
We had some parts in stock at a warehouse; unfortunately, we had not rust-protected these parts, and when we opened our crate we found rust had made these parts not functional. We also felt that because of the mechanical failure we should replace the entire crankcase, because of the potential for metal particles to cause a future bearing failure.
In phone discussions with Jarrod, we agreed that the best course of action was for us to send the parts we had back to PDC, to see if the rusted parts could be fixed. PDC was going to see how quickly they could provide us with a new crankcase. We knew at this point there was a crankcase close to ready but it needed to be finished and painted.
On Saturday I called Garry Gallo, our longtime salesperson. Garry answered the phone, even though he was on vacation, it was Saturday, and he was at a car show. Garry told me that they were working on it, but for more up-to-date information he gave me the cell number for Tom Greco.
When I first spoke to Tom early on Saturday, he said that he had people working on everything, but he was not sure if we would be able to get all the parts on Monday.
I spoke to Tom later in the day Saturday and was extremely relieved to hear that the parts would all be ready and driven to our site on Monday, with Wayne to help us rebuild the units.
I came in early (for me) on Monday at 7:30 am and found out that Wayne had arrived at our site just before 6:00 am on Monday and had been showing our maintenance team how to install the pistons, piston rings, and rider rings in the sleeves. Wayne must have left before 3:00 am to arrive at our site with the parts that early!
Wayne not only helped us rebuild the compressors but also took the time to teach our maintenance team the right way to rebuild each component and the reasons it was important to do it that way.
Wayne also showed us a much better way to prime the compressors, cutting our time from four hours to about 15 minutes.
Your team’s incredible response during this event, combined with how well PDC compressors have performed for us over the last 14 years, will continue to ensure that PDC Machines is our preferred compressor supplier.
Refrigeration and Oxygen Company, Ltd
We are using a couple of PDC compressors and are quite satisfied with the performance and after-sales services.
Timo Mutka, McPhy
PDC supplied several hydrogen compressors to McPhy, mainly for hydrogen refueling stations and also for industrial applications. The quality of the technical advice during the design and construction phases, the good respect of the agreed schedule, and the effectiveness of the after-sales are particularly appreciated. PDC has been a great partner in the development of McPhy.
Tom Skoczylas, Director of Applications Engineering, Proton
Proton Energy Systems Inc. d/b/a Proton Onsite has installed numerous compressors from PDC for hydrogen service in various locations and applications all around the world since about 2006. Some of them are located in extreme environments such as deserts and coastlines. Our experience shows that the compressors are extremely reliable and in the rare occasion they are in need of any service, the support from PDC is terrific.
Michael G. Dray, CSULA College of Engineering
We publicly acknowledge PDC’s expertise and contributions to the success of the largest university H₂ facility in the nation. The U.S. Dept of Energy, CA Energy Commission, National Labs and many others were informed of PDC’s role, and there were several hundred hydrogen industry supporters present. Please accept my personal thanks and convey Cal State University Los Angeles’ appreciation to your colleagues at PDC.
Mark Schultz, HydraFLX Systems
HydraFLX Systems LLC has been a DLA (Defense Logistics Agency) registered consultant and defense contract actuary since 2001, specializing in innovative research and development of gaseous fuel technologies and early commercialization of hydrogen and fuel cells.
Under a memorandum of understanding between the United States Air Force and the State of Hawaii, HydraFLX was selected to stand up the National Demonstration Center for hydrogen and renewable technologies at Joint Base Pearl Harbor Hickam in Hawaii, to advance the use of hydrogen in military ground support and commercial applications, drive down the cost of safe, deployable infrastructure, and develop seamless integration with renewable energy. Three hydrogen technologies initially demonstrated at JBPHH are used in commercial markets today.
We have tested and demonstrated five gas compressors over ten years at the research site. The two PDC Machines hydrogen gas compressors have outperformed all competitors in our three main categories of analysis: electrical efficiency, through-put gas flow efficiency, and cost. We are extremely pleased with PDC’s trouble-free operation and ease of maintenance. In four years’ time, we had but one minor issue with one of the units and found that PDC’s factory support is second to none. We were back up and running in no time. Their factory floor technical folks are first class.
HydraFLX cannot more highly recommend PDC Machines to anyone seeking high-quality, long-lasting equipment that is as durable as it is easy to operate. Their automation team obviously has abundant experience putting together custom machines and integrating them with different dispensers, high-pressure storage and pressure management safety systems.
The Linde Group
PDC Machines has been an integral supplier of diaphragm compressor systems and piping skids to Linde for more than a decade.
Their ability to tailor a packaged solution extends well beyond the robust compressor to include UL panel fabrication, navigating U.S. and foreign electrical/mechanical code requirements, PLC control systems, and vessel code stamping. And with their extensive machine shop and two fabrication facilities, PDC Machines has the ability to tightly manage our project’s safety, budget, and schedule goals.
After commissioning, their exemplary customer service comes to the forefront with same-day spare parts shipments and technical support, at any time of day.
PDC Machines is a solid top-tier supplier.
Airgas
Airgas considers PDC Machines a preferred vendor for compressors. They are listed in our National Resource Manual, which covers all the Airgas plant operations. PDC Machines has shown they are a very reliable vendor.
We have been using their compressors for transferring product from our tube trailers to cylinders in our Airgas plants for over 11 years. We have found their compressors to be very reliable, which is critical to serving our customers in a timely manner.
Last but most important is the ability to provide good quality customer service, which PDC Machines has always achieved for Airgas. Their machines arrive as promised, parts are prompt, and their technical support is there when you need it.
(There are 12 Airgas locations across the United States using PDC Machines products).
Sandip, Olein Recovery
I am using PDC compressor since last 15 years. Olein is very happy about compressor performance, technical support, parts availability, and main thing is that compressor run safely without any incident. I am using this compressor for hydrogen compression application.
Sandip
Olein Recovery
Bennett Waterhouse, Air Liquide
I am taking the time to write this thank-you letter to PDC because of the incredible customer support we received when we were in need.
I have never had to ask PDC to do any service or rush any parts on any of the 6 PDC compressors I have bought in the last 14 years. This is because your units have always run as expected and we have always had your recommended critical parts in stock. We had never previously experienced a failure on any of these units.
Our recent crisis came about because of an undiagnosed failure of our heat tracing, combined with a concurrent process upset. These conditions led to extreme cold, causing compressor oil thickening, causing higher than normal vibration. These excessive vibrations led to an unrecognized oil leak. The oil leak eventually caused cavitation in one of the compressors, which led to a failure of lower end parts.
We were not able to properly diagnose this problem until we had Wayne come out to our site. He led us through a regimented troubleshooting approach, which led us to find that we needed to replace the entire lower end and crankcase. This was, of course, on a Friday afternoon.
This failure showed the main safety and quality reason that we use your diaphragm compressors, even with a lower end mechanical failure, caused by cavitation, leading to extreme vibration; we never experienced any process leaks to atmosphere or any mixing of oil and process gas.
We had some parts in stock at a warehouse; unfortunately, we had not rust-protected these parts, and when we opened our crate we found rust had made these parts not functional. We also felt that because of the mechanical failure we should replace the entire crankcase, because of the potential for metal particles to cause a future bearing failure.
In phone discussions with Jarrod, we agreed that the best course of action was for us to send the parts we had back to PDC, to see if the rusted parts could be fixed. PDC was going to see how quickly they could provide us with a new crankcase. We knew at this point there was a crankcase close to ready but it needed to be finished and painted.
On Saturday I called Garry Gallo, our longtime salesperson. Garry answered the phone, even though he was on vacation, it was Saturday, and he was at a car show. Garry told me that they were working on it, but for more up-to-date information he gave me the cell number for Tom Greco.
When I first spoke to Tom early on Saturday, he said that he had people working on everything, but he was not sure if we would be able to get all the parts on Monday.
I spoke to Tom later in the day Saturday and was extremely relieved to hear that the parts would all be ready and driven to our site on Monday, with Wayne to help us rebuild the units.
I came in early (for me) on Monday at 7:30 am and found out that Wayne had arrived at our site just before 6:00 am on Monday and had been showing our maintenance team how to install the pistons, piston rings, and rider rings in the sleeves. Wayne must have left before 3:00 am to arrive at our site with the parts that early!
Wayne not only helped us rebuild the compressors but also took the time to teach our maintenance team the right way to rebuild each component and the reasons it was important to do it that way.
Wayne also showed us a much better way to prime the compressors, cutting our time from four hours to about 15 minutes.
Your team’s incredible response during this event, combined with how well PDC compressors have performed for us over the last 14 years, will continue to ensure that PDC Machines is our preferred compressor supplier.
Refrigeration and Oxygen Company, Ltd
We are using a couple of PDC compressors and are quite satisfied with the performance and after-sales services.
Timo Mutka, McPhy
PDC supplied several hydrogen compressors to McPhy, mainly for hydrogen refueling stations and also for industrial applications. The quality of the technical advice during the design and construction phases, the good respect of the agreed schedule, and the effectiveness of the after-sales are particularly appreciated. PDC has been a great partner in the development of McPhy.
Tom Skoczylas, Director of Applications Engineering, Proton
Proton Energy Systems Inc. d/b/a Proton Onsite has installed numerous compressors from PDC for hydrogen service in various locations and applications all around the world since about 2006. Some of them are located in extreme environments such as deserts and coastlines. Our experience shows that the compressors are extremely reliable and in the rare occasion they are in need of any service, the support from PDC is terrific.
Michael G. Dray, CSULA College of Engineering
We publicly acknowledge PDC’s expertise and contributions to the success of the largest university H₂ facility in the nation. The U.S. Dept of Energy, CA Energy Commission, National Labs and many others were informed of PDC’s role, and there were several hundred hydrogen industry supporters present. Please accept my personal thanks and convey Cal State University Los Angeles’ appreciation to your colleagues at PDC.
Mark Schultz, HydraFLX Systems
HydraFLX Systems LLC has been a DLA (Defense Logistics Agency) registered consultant and defense contract actuary since 2001, specializing in innovative research and development of gaseous fuel technologies and early commercialization of hydrogen and fuel cells.
Under a memorandum of understanding between the United States Air Force and the State of Hawaii, HydraFLX was selected to stand up the National Demonstration Center for hydrogen and renewable technologies at Joint Base Pearl Harbor Hickam in Hawaii, to advance the use of hydrogen in military ground support and commercial applications, drive down the cost of safe, deployable infrastructure, and develop seamless integration with renewable energy. Three hydrogen technologies initially demonstrated at JBPHH are used in commercial markets today.
We have tested and demonstrated five gas compressors over ten years at the research site. The two PDC Machines hydrogen gas compressors have outperformed all competitors in our three main categories of analysis: electrical efficiency, through-put gas flow efficiency, and cost. We are extremely pleased with PDC’s trouble-free operation and ease of maintenance. In four years’ time, we had but one minor issue with one of the units and found that PDC’s factory support is second to none. We were back up and running in no time. Their factory floor technical folks are first class.
HydraFLX cannot more highly recommend PDC Machines to anyone seeking high-quality, long-lasting equipment that is as durable as it is easy to operate. Their automation team obviously has abundant experience putting together custom machines and integrating them with different dispensers, high-pressure storage and pressure management safety systems.
The Linde Group
PDC Machines has been an integral supplier of diaphragm compressor systems and piping skids to Linde for more than a decade.
Their ability to tailor a packaged solution extends well beyond the robust compressor to include UL panel fabrication, navigating U.S. and foreign electrical/mechanical code requirements, PLC control systems, and vessel code stamping. And with their extensive machine shop and two fabrication facilities, PDC Machines has the ability to tightly manage our project’s safety, budget, and schedule goals.
After commissioning, their exemplary customer service comes to the forefront with same-day spare parts shipments and technical support, at any time of day.
PDC Machines is a solid top-tier supplier.
Airgas
Airgas considers PDC Machines a preferred vendor for compressors. They are listed in our National Resource Manual, which covers all the Airgas plant operations. PDC Machines has shown they are a very reliable vendor.
We have been using their compressors for transferring product from our tube trailers to cylinders in our Airgas plants for over 11 years. We have found their compressors to be very reliable, which is critical to serving our customers in a timely manner.
Last but most important is the ability to provide good quality customer service, which PDC Machines has always achieved for Airgas. Their machines arrive as promised, parts are prompt, and their technical support is there when you need it.
(There are 12 Airgas locations across the United States using PDC Machines products).
Sandip, Olein Recovery
I am using PDC compressor since last 15 years. Olein is very happy about compressor performance, technical support, parts availability, and main thing is that compressor run safely without any incident. I am using this compressor for hydrogen compression application.
Sandip
Olein Recovery
Enviromental, Social and Governance
Environmental
In 2021 alone, PDC Machines supported the reduction of 600k tons of CO₂ with hydrogen refueling. Additionally, PDC supported the opening of various hydrogen stations, including a station for the University of Illinois, Urbana-Champaign. This project will save 15k gallons of diesel fuel per year. PDC compressors also fueled the green hydrogen buses and fuel cell vehicles that ferried athletes and visitors to and from the 2022 Beijing Winter Olympics, a massive undertaking that saved thousands of passengers’ worth of diesel fuel and greenhouse gases.
While greenhouse gases and their contribution to climate change are often the major factor when measuring environmental impact, PDC is also committed to stewardship of the local environment. This extends from continual testing and usage of more environmentally friendly products around our manufacturing facilities, to extensive recycling and use of scrap metal, preventing these refined materials from polluting local water or contributing to landfills.
Social
Under the leadership of the founding Afzal family, PDC Machines strives to create a company culture that works for all its employees and represents the makeup of our local areas. PDC’s Executive Board is composed of professionals from a variety of backgrounds, and our workforce is a reflection of our commitment to diversity, equity, and inclusion. Through high-quality jobs with significant opportunity for advancement, PDC has been able to serve communities disproportionately affected by the bias in hiring and pay gaps that plague other companies. We take great pride in this fact.
In service of creating a thriving company culture, PDC involves employees in the process of decision making. Beginning in 2021, leadership began running focus groups composed of PDC employees with one goal – listening intently. Afterwards, teams were created and led by volunteer employees to execute feedback in a sustainable way. These Action Committees work in service of improving life at PDC for all employees, from the micro to macro levels. At PDC, we believe empowering employees with real decision-making ability endows our workforce with a real sense of agency, improving quality of life and employee retention.
PDC Machines is deeply involved in our community. PDC sponsors the local food kitchen, Manna on Main, in their annual Race to End Hunger. “PDC Machines has supported Manna on Main Street, a nonprofit serving households experiencing food insecurity, for over 10 years,” said Suzan Neiger Gould, executive director of Manna. “In that time, they have provided critical financial support and leadership in projects that have moved Manna from a small, community organization to a regional leader in the hunger and food safety net system.”
Governance
PDC's governance reflects our values as a company, ensuring 100% transparency of decision making, enforcement of anti-harassment training, and compliance with stringent cybersecurity guidelines. This ensures the safety of our employees and company at all levels.
As one of Arcline Investment Management’s portfolio companies, we also enjoy the support and governance from their veteran board.
For any questions about PDC’s ESG guidelines and commitments, please contact Jesse Goldberg